Alcast Company Things To Know Before You Buy
Table of ContentsAll About Alcast CompanyFascination About Alcast CompanyThe Best Strategy To Use For Alcast CompanyThe Best Strategy To Use For Alcast CompanyHow Alcast Company can Save You Time, Stress, and Money.The Ultimate Guide To Alcast Company
The refined distinction depends on the chemical content. Chemical Comparison of Cast Aluminum Alloys Silicon promotes castability by minimizing the alloy's melting temperature level and enhancing fluidity during casting. It plays an essential function in enabling intricate molds to be filled accurately. Furthermore, silicon adds to the alloy's toughness and use resistance, making it important in applications where sturdiness is crucial, such as automotive parts and engine elements.It also boosts the machinability of the alloy, making it easier to process into completed products. In this means, iron contributes to the total workability of light weight aluminum alloys.
Manganese adds to the toughness of light weight aluminum alloys and enhances workability. Magnesium is a light-weight element that gives stamina and impact resistance to light weight aluminum alloys.
Some Known Details About Alcast Company
Zinc boosts the castability of aluminum alloys and aids control the solidification procedure during casting. It improves the alloy's stamina and hardness.
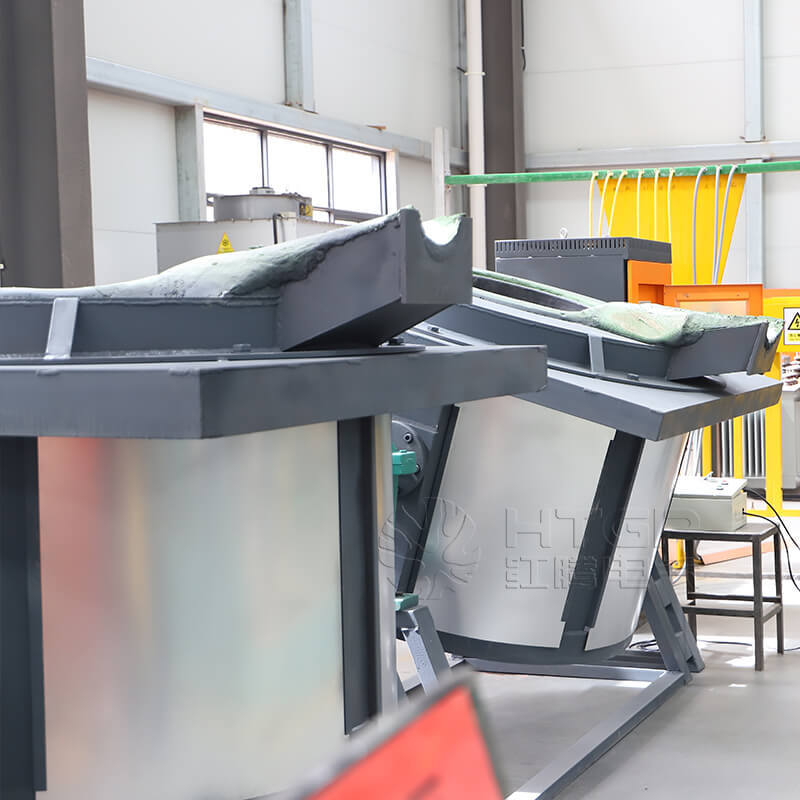
The main thermal conductivity, tensile stamina, yield strength, and prolongation vary. Among the above alloys, A356 has the greatest thermal conductivity, and A380 and ADC12 have the least expensive.
Excitement About Alcast Company

In accuracy spreading, 6063 is well-suited for applications where complex geometries and high-quality surface area coatings are paramount. Instances consist of telecommunication enclosures, where the alloy's exceptional formability enables smooth and aesthetically pleasing layouts while keeping architectural stability. In a similar way, in the Lighting Solutions market, precision-cast 6063 parts produce elegant and efficient lights fixtures that require complex shapes and good thermal performance.
It results in a better surface finish and better rust resistance in A360. The A360 displays superior elongation, making it perfect for complex and thin-walled components. In accuracy spreading applications, A360 is appropriate for sectors such as Consumer Electronic Devices, Telecommunication, and Power Devices. Its boosted fluidness permits elaborate, high-precision elements like mobile phone coverings and communication gadget real estates.
How Alcast Company can Save You Time, Stress, and Money.
Its distinct residential properties make A360 a valuable option for precision spreading in these sectors, boosting item sturdiness and high quality. Casting Foundry. Light weight aluminum alloy 380, or A380, is a widely used spreading alloy with numerous unique features.
In accuracy casting, light weight aluminum 413 radiates in the Consumer Electronic Devices and Power Equipment industries. It's commonly utilized to craft intricate components like smart device housings, cam bodies, and power device housings. Its accuracy is remarkable, with tight tolerances approximately 0.01 mm, guaranteeing flawless product setting up. This alloy's exceptional rust resistance makes it a superb option for outside applications, ensuring lasting, durable items in the pointed out sectors.
The Best Guide To Alcast Company
When you have actually chosen that the light weight aluminum die casting process is ideal for your job, an essential next action is choosing one of the most proper alloy. The aluminum alloy you choose will considerably affect both the spreading procedure and the buildings of the end product. Because of this, you must aluminum casting manufacturer make your decision carefully and take an educated approach.
Figuring out the most suitable light weight aluminum alloy for your application will suggest evaluating a vast selection of features. The very first category addresses alloy attributes that influence the manufacturing procedure.
How Alcast Company can Save You Time, Stress, and Money.
The alloy you choose for die casting directly impacts a number of aspects of the casting process, like how simple the alloy is to function with and if it is vulnerable to casting flaws. Warm fracturing, additionally called solidification cracking, is a common die spreading defect for light weight aluminum alloys that can lead to interior or surface-level splits or cracks.
Certain light weight aluminum alloys are a lot more at risk to hot fracturing than others, and your choice must consider this. An additional typical defect located in the die casting of aluminum is pass away soldering, which is when the cast stays with the die walls and makes ejection difficult. It can harm both the actors and the die, so you ought to look for alloys with high anti-soldering buildings.
Rust resistance, which is currently a noteworthy characteristic of aluminum, can vary significantly from alloy to alloy and is an important characteristic to consider depending upon the ecological conditions your item will certainly be revealed to (Casting Foundry). Put on resistance is one more residential property typically sought in light weight aluminum items and can distinguish some alloys